Continental unveils LD-Master L5 Traction construction tyre with integrated self-monitoring
Construction machines usually operate with heavy payloads and are exposed to a variety of harsh ground conditions, such as rock, gravel, or rubble. The LD-Master L5 Traction is specifically designed for loaders operating on abrasive surfaces and in face working jobs where high productivity and assured vehicle uptime are of most importance.
The reinforced 3* carcass is said to satisfy the highest load carrying capacity requirements, even under extensive production cycles. The L5 traction tread pattern protects the carcass and ensures smooth and safe operation on the construction site.
The solid tread block design always provides secure traction. The extra deep tread and sidewall protection are also said by Continental to make the tyre more robust and ensure long-term productivity.
To minimise idle time and ensure serviceability even under harsh conditions, the special tires fitted to construction machinery should be controlled as precisely as possible.
The LD-Master L5 Traction is fitted with an integrated tyre sensor, making monitoring possible in real time. The sensor monitors temperature and tyre pressure, said to assure the most efficient operation mode for a long tyre life.
In addition to the LD-Master L5 Traction, Continental is presenting its EM-Master E3/L3 as 65-series for construction/surface applications and a sneak preview for a new solid skid-steer tyre.
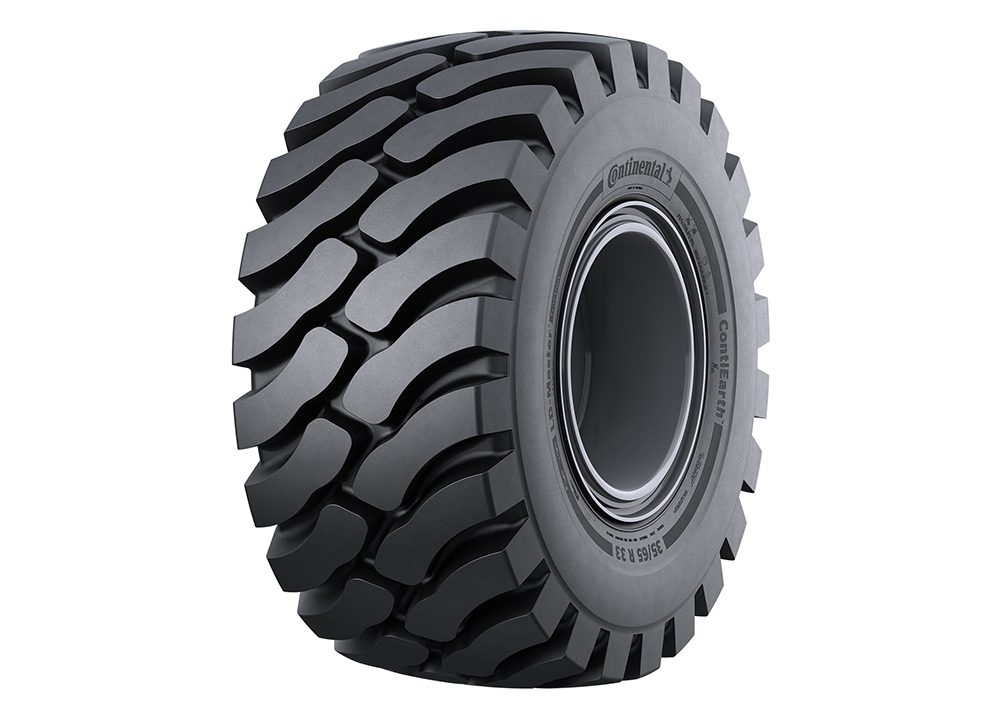