Tunnelling technology award for Herrenknecht
The award was given for the next innovation boost in the mechanised production of tunnel infrastructure in soft ground formations with and without water-bearing layers.
Using the latest technology for continuous tunnelling results in a significant reduction in construction times for longer tunnel sections. This new development is already being used in a high-impact mobility project in Europe.
Dr-Ing E Martin Herrenknecht, founder and CEO of the firm commented, "Continuous tunnelling is the next significant innovation step in mechanised tunnelling. New underground traffic routes have to be built ever faster.
“Continuous tunnelling gives clients and contractors a decisive time advantage that ultimately benefits the entire project and all partners involved. Rail, metro and road tunnels can be built and put into operation significantly faster."
Until now, mechanised tunnelling with shield machines in soft ground has always been a stop-and-go sequential process. Each excavation stroke is followed by the ring building sequence, so that the excavation has to pause and the driving cycle only restarts when the next segmental ring has been installed. These interruptions to tunnel advance in soft ground formations cost time over longer distances.
In contrast, a continuous tunnelling process where machines continue excavation while the lining rings are being installed can contribute to considerable savings in construction time.
The new continuous tunnelling system developed by Herrenknecht can deliver an increase in efficiency during tunnel construction. In continuous tunnelling, the thrust cylinders that push the machine forward during advance take over the force share of the cylinders that are retracted for ring building.
To ensure that the machine maintains course, the centre of thrust resulting from the combined driving forces of the applied thrust cylinders must remain unchanged in its position. At the heart of continuous tunnelling is a powerful computer system and process-specific software programs that can calculate the necessary pressures in the thrust cylinders. It ensures that the machine operator controls the tunnel boring machine along the specified alignment.
In continuous advance, the machine operator no longer controls the pressures in the thrust cylinders manually using rotary controls (potentiometers) on the control panel. The Centre of Thrust (CoT) system helps the shield operator to control the machine.
The system consists of a display panel that shows the operator the current position of the centre of pressure and on which he selects the desired position of the centre of thrust. The control of the thrust cylinders is handled by algorithms in the computer system.
Compared to manual control by potentiometers, the CoT maintains the specified alignment more efficiently and effectively. The CoT system can increase total tunnelling performance by a factor of up to 1.6 compared to the previous discontinuous method, delivering a significant reduction in construction time for long tunnels.
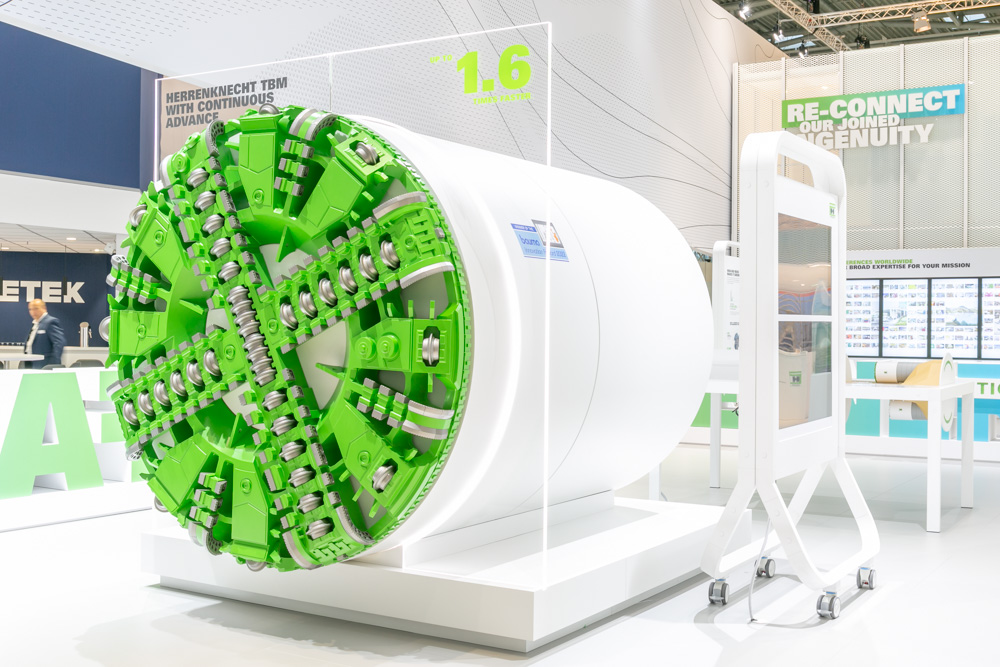