Advanced travel microsimulation from SYSTRA
SYSTRA is introducing a sophisticated Paramics Discovery 26 package that offers new capabilities for active travel microsimulation. The software now includes cyclist modelling and pedestrian visualisation capability.
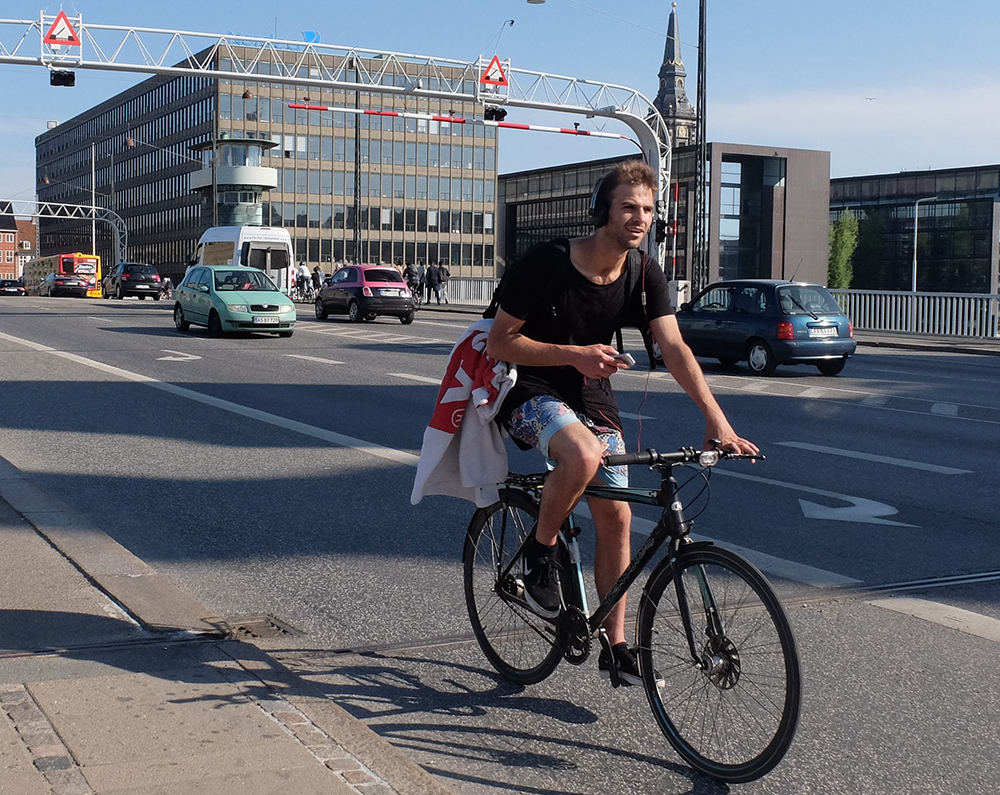