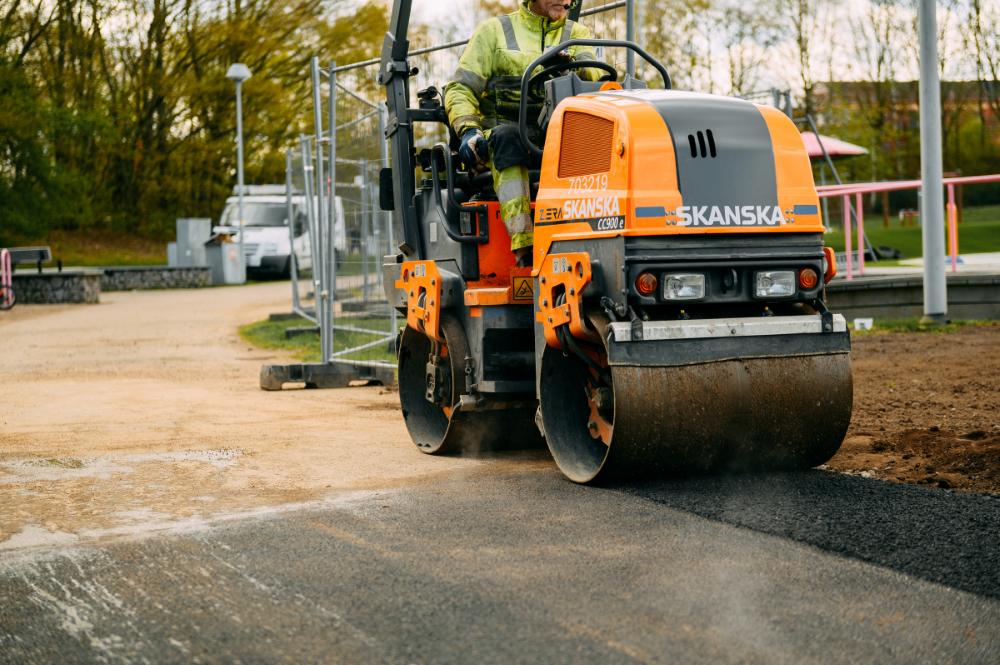
Equipment from Dynapac is allowing contractor Skanska to carry out compaction without emissions. The contractor has been trialling Z.ERA CC900 e tandem vibratory rollers from Dynapac.
The performance of the electric machines was put to the test during its deployment with Skanska ine. Charging was said to be easy and quick in public and easy-to-reach locations such as filling stations and local charging ports.
Skanska personnel also said that the electric compactors matched the performance of conventional diesel units, with no differences in compaction results.
“The battery lasts longer than expected. We didn't think it would perform that long before it ran out. And we really pushed it to its limits last winter. Then we compacted almost 100tonnes but only needed to charge it while having lunch,” said a Skanska operator.
The Z.ERA CC900 e weighs in at 1.7tonnes and has an operating width of 0.9m. Its double-drum vibratory roller has been designed to meet the needs of utility contractors and rental fleet operators while delivering the same linear load, amplitude, frequency, and travel speed as Dynapac’s comparable diesel-powered model. Aside from zero-emissions, the Z.ERA CC900 e offers reduced noise levels and maintenance checks due to battery-power.