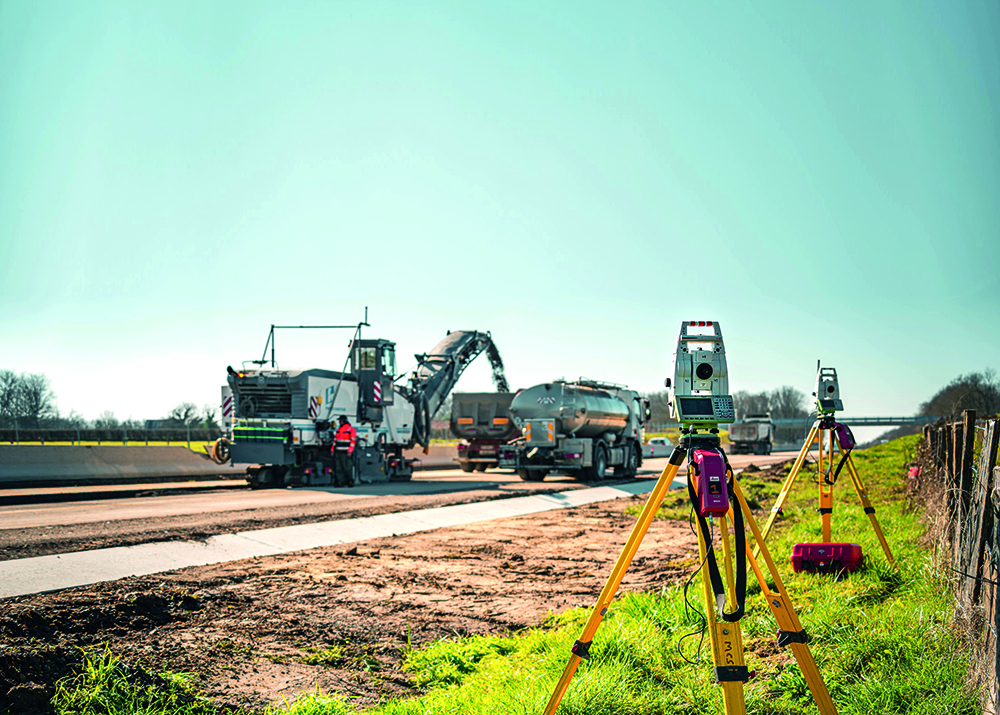
A contractor in France has utilised the latest machine control technology to deliver high-quality road milling for a key project.
The firm, 2AGE-MCS, has had a very successful collaboration with Leica Geosystems on the RCEA (Route Centre-Europe Atlantique) project in central France. Using machine control solutions from Leica Geosystems, 2AGE-MCS delivered high-quality milling results that left no room for error and also stayed ahead of the tight schedule demanded for the project.
On road construction projects, precision and speed are key factors for all involved. For contractors and operators who manage complex projects, cutting-edge technology can help keep everything on track.
The job required milling 4km of road in just two days, a major challenge for any contractor. This formed part of the RCEA project, a major infrastructure initiative to enhance one of France’s critical traffic routes. The Roger Martin Group entrusted 2AGE-MCS with the responsibility of carrying out the precise and swift milling work for the RCEA road expansion between Paray and Charolles, guaranteeing the road surface met top safety and quality standards.
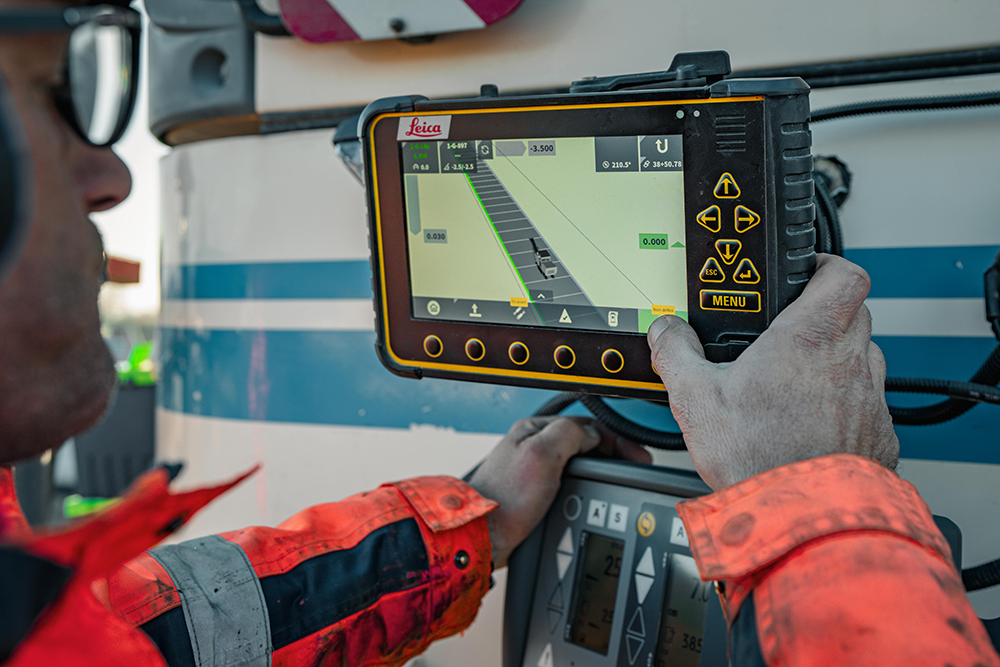
The pressure was not only to finish the job in time but also to do it with such precision that the asphalt mix would also be laid precisely over the milled surface. The contractor achieved this using the latest 3D machine control.
"Leica Geosystems’ machine control solutions have truly proven their worth," said Bastien Lambert, director of 2AGE-MCS. Equipped with the Leica MC1 3D milling solution, mounted on a Wirtgen W 210 XP cold milling machine, the team was able to meet the tough schedule while delivering the high-quality performance required.
The system followed the predefined 3D models very closely, ensuring that the surface was millimetre-accurate once the milling bits passed over the surface. This level of accuracy reduced the need for follow-up corrections, saving both time and money.
The setup of the system was significantly less complex and time consuming than the contractor anticipated. Thanks to the sophisticated yet easy to use technology, the Leica MC1 system was up and running in just 20 minutes. This quick setup allowed the team to start milling right away, a critical factor given their tight schedule.
Speed was not the only benefit either as the technology also delivered intelligent systems. Leica’s technology features an automatic device-switching feature, called Leica 1-Up system, which saved the team even more time by reducing manual interventions. This tool switches automatically between different total stations without requiring manual intervention, a benefit that significantly reduces downtime and potential errors. By allowing continuous machine guidance, this system ensures that the milling process remains consistently accurate, even over long distances.
As Bastien Lambert, Director of 2AGE-MCS, pointed out, "This functionality saved us considerable time," highlighting its critical role in maintaining high-quality results throughout the project. To maximise the system's effectiveness, Lambert's team positioned four total stations every 125m, enabling real-time monitoring and control that kept the milling operation precisely on track from start to finish.
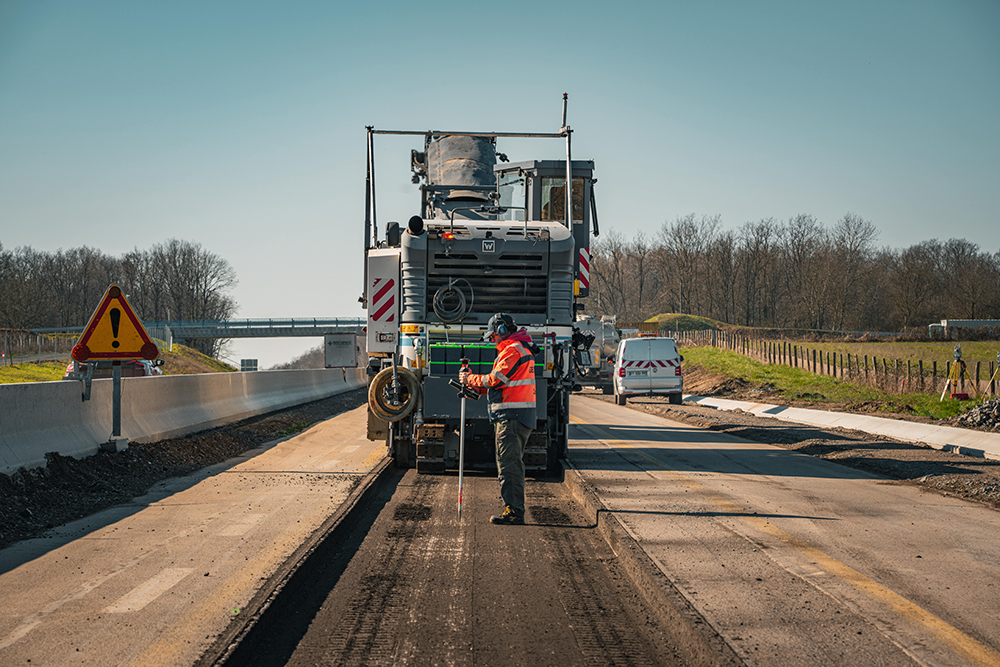
As the team milled away, real-time data streamed from the total stations to the milling machine at 10Hz. That means the machine made tiny corrections ten times/second to stay on course. This kind of high frequency adjustment is like having a super accurate autopilot guiding the machine, ensuring that the final road surface is as smooth as a runway.
"Without 3D guidance, this would have been impossible. Manual measurement would have significantly reduced our precision and speed," Lambert acknowledged.
In just two days, 2AGE-MCS milled approximately 1,500tonnes of road surface, moving at a steady pace of about 12m/min. As a result, the contractor was able to achieve an accurately milled road that meets all regulatory standards and is ready for the next phase of the project. Thanks to the synergy between 2AGE-MCS’s expertise and Leica Geosystems’ cutting-edge technology, the project was a resounding success.
When it comes to large-scale infrastructure projects, investing in 3D machine control solutions can be the difference between hitting a deadline with precision or falling short.
The contractor, Roger Martin Group was impressed with the accuracy and the short amount of time the job was delivered. Anthony Teriele from Roger Martin commented, “We selected 2AGE-MCS due to their proven expertise and our need for high precision and rapid implementation."
As Lambert put it, "Leica Geosystems’ solutions have been instrumental in achieving our goals swiftly and accurately. Their technology has truly enhanced our operational efficiency and precision."